Understanding Mold Sweat and Its Impact on Manufacturing
- Heat Tech Systems
- May 22
- 3 min read
Updated: 7 days ago
Mold sweat is a common issue in manufacturing that can significantly compromise the quality of parts. It occurs when the mold's surface temperature falls below the dew point of the surrounding air, resulting in condensation. This condensation creates moisture on the mold's surface, leading to defects in finished products and potential damage to the mold itself. In this article, we will explore the causes of mold sweat, effective prevention strategies, and its overall impact on the quality of your manufactured parts.
Causes of Mold Sweat
Humid Environment
One of the leading causes of mold sweat is a humid environment. High humidity levels can result in condensation forming on molds. According to the National Oceanic and Atmospheric Administration (NOAA), a relative humidity level above 60% significantly increases the likelihood of condensation. This problem often becomes more pronounced during warmer seasons or in consistently humid climates.
Increased moisture in the air can reduce the overall efficiency of the molding process. For example, during a humid summer day, production rates may drop by as much as 15% due to condensation-related defects.
Chiller Temperatures
In addition to humidity, chiller temperatures set too low can also contribute to mold sweat. Chillers are essential for cooling molds during the injection molding process. If chillers are set below the dew point of the surrounding air, condensation will undoubtedly occur. The ideal cooling temperature typically ranges from 50°F to 60°F (10°C to 15°C).
A study conducted in 2019 revealed that 30% of manufacturers faced issues with condensation due to excessively low chiller temperatures. This not only increases downtime but also leads to costly repairs in the future.
Solutions for Mold Sweat
Increase Mold Temperature
Raising the mold temperature often serves as an effective method to combat mold sweat. By ensuring the mold temperature is above the dew point, manufacturers can substantially reduce or even eliminate condensation. This can be achieved by adjusting heating elements or utilizing temperature controllers effectively.
For instance, manufacturers have successfully increased their mold temperatures by just 5°F (2.8°C), resulting in a remarkable 25% reduction in defects related to condensation.
Adjust Cycle Time
Modifying the cycle time of the molding process can also help mitigate mold sweat. Operating a mold at a warmer temperature while extending the cycle time facilitates better heat retention, which reduces moisture buildup. This approach allows plastic to flow more efficiently, minimizing the chances of condensation.
Manufacturers who adopted this change reported improved productivity, with cycle times decreasing by 20% without compromising part quality.
Improve Venting
Proper venting of the mold is essential for successful operations. Adequate venting allows trapped air to escape as plastic fills the mold, substantially reducing moisture buildup and the likelihood of condensation. Techniques such as increasing the size of venting channels or adding additional vents can significantly enhance mold efficiency and the quality of finished parts.
Control Humidity
Maintaining optimal humidity levels around the mold is critical for effective manufacturing. Manufacturers should consider utilizing dehumidifiers to keep humidity levels below 50%. This simple yet effective measure can drastically reduce the risk of mold sweat, thereby improving product quality and overall operational efficiency.
Impact of Mold Sweat
Mold sweat can have serious implications, particularly regarding the quality of finished parts. Even a slight amount of moisture can lead to defects like splay marks or surface imperfections, adversely affecting both aesthetic and functional aspects of the final product. Studies show that parts exhibiting minor defects can result in customer dissatisfaction, potentially leading to revenue loss ranging from 5% to 10%.
Moreover, mold sweat can be damaging to the mold itself. Prolonged moisture exposure can cause corrosion, significantly diminishing mold performance and lifespan. Manufacturers may encounter remediation costs that range from $2,000 to over $20,000, depending on the extent of the damage.
For these reasons, addressing mold sweat is crucial for maintaining high-quality standards and prolonging the life of manufacturing equipment.
Conclusion
Effectively understanding mold sweat is vital for manufacturers aiming to enhance product quality and maintain process efficiency. By identifying causes such as humid conditions and low chiller temperatures, manufacturers can implement practical solutions. These solutions include increasing mold temperature, adjusting cycle times, improving venting, and controlling humidity levels.
The consequences of mold sweat extend beyond product quality; they can also lead to mold damage over time. By proactively managing mold sweat, manufacturers can boost product quality, decrease defect rates, and extend the lifespan of their equipment.
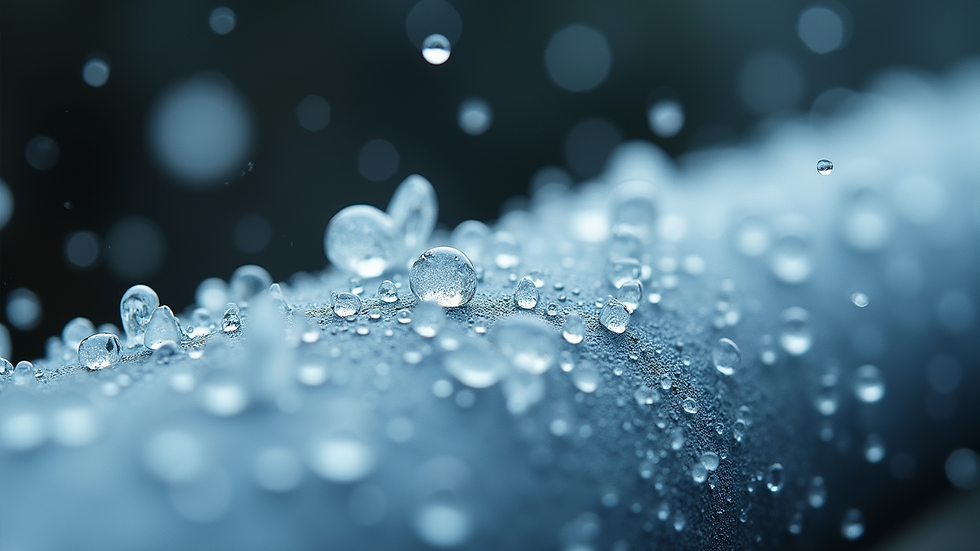
Understanding and effectively managing mold sweat is essential for successful manufacturing processes.
Please contact us at www.plasticmoldcleaners.com for more information. We are here to help!
Comments